Today, marginal gains are often weaponised against consumers, distracting from the fundamentals that truly make us faster, and justifying products of questionable value. In the race to optimise every aspect of speed, aerodynamics, and weight, the compromises made along the way can lead to unintended consequences: fragile equipment, reduced durability, higher costs, and sometimes, slower real-world performance.
This is part two of a series investigating the dark side of marginal gains. Here, we examine when the pursuit of optimisation stops being an advantage and starts becoming a liability, from bike fit issues and injury risk to psychological pressure and the hidden costs of chasing ever-smaller gains.
Lighter, stiffer, faster and less durable
For the longest time weight was the primary performance metric by which a bike was measured. Aero hit the big time in the ‘90s under Chris Boardman, Miguel Indurain and others, but the aero revolution truly didn’t hit the consumer market until a decade or more later. The drive for marginal gains in aerodynamics and weight savings is perhaps most noticeable in the “latest and greatest” aero bikes. We often laugh or roll our eyes when a brand trots out the classic “lighter, stiffer, faster” claim, but the reality is, those are still the levers through which performance is marketed and measured.
It’s confusing and frustrating, as we delved into in part one of this series, but it’s not just manufacturers or marketing teams driving the problem; often it’s often our own appetite for “lighter, stiffer, faster” that pushes brands to ever more extreme lengths to prove each new model is better than the last. But there’s a breaking point, sometimes literally, where the gains become increasingly marginal, costly, and riddled with compromises or unintended consequences.
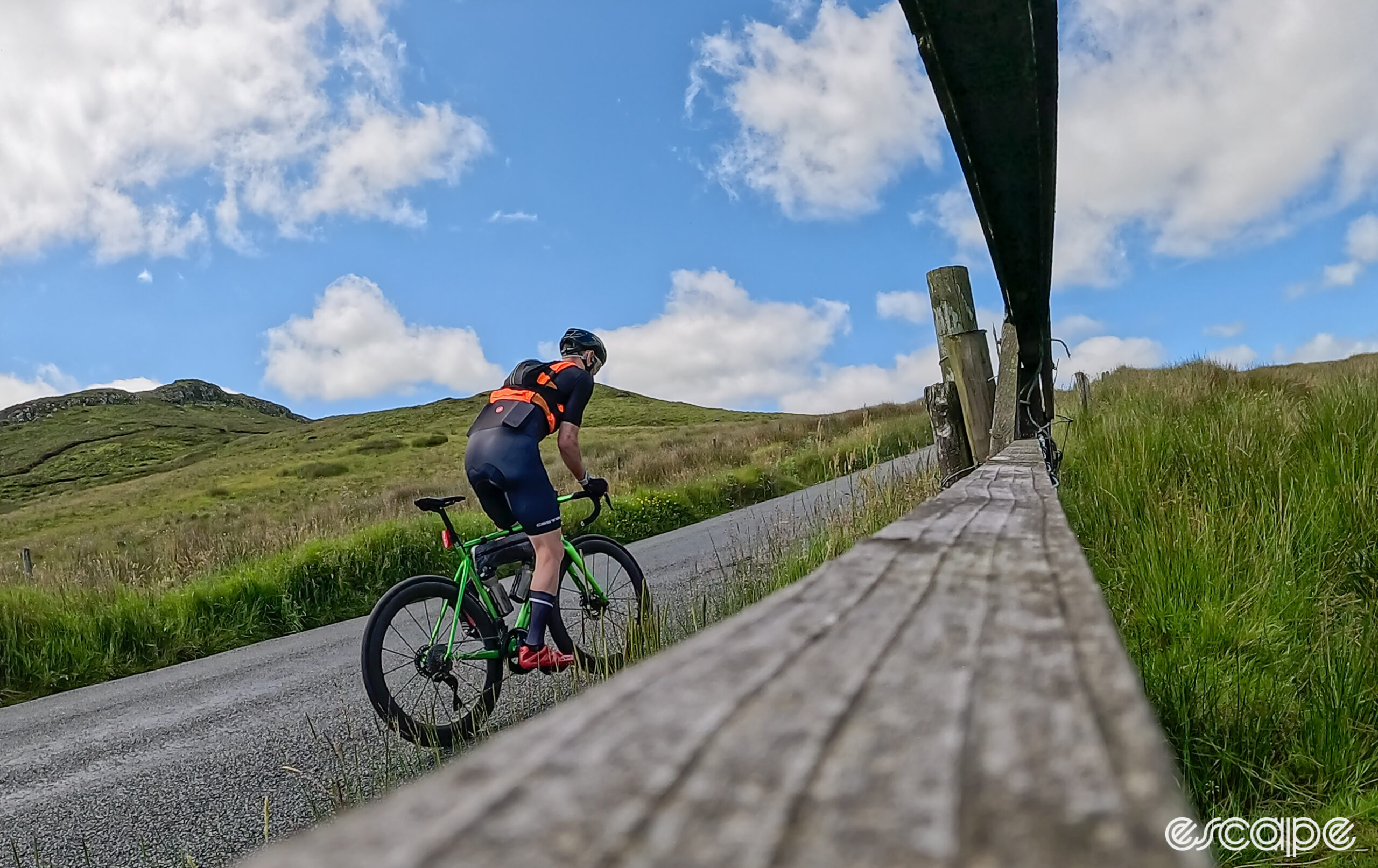
How so? With the low-hanging fruit long gone, manufacturers face mounting pressure to deliver ever more marginal improvements. Chasing lighter, stiffer, and faster at all costs often leads to increasingly complex, fragile, and rider-unfriendly designs. As the performance bar rises, the compromises deepen, and the gains become more and more complex.
The sheer number of stop-ride notices and recalls on equipment in the past few years is all the evidence one should need to understand these performance-led improvements are neither simple to deliver nor, one could argue, conducive to overall better bikes.
Fork steerer recalls are perhaps the most glaring and alarming example. With manufacturers employing all manner of methods to integrate cable routing for both improved aero and a clean aesthetic, we’ve seen too many brands have to recall designs that are failing in use.
And it’s not just fork steerers. From frames to wheels to components, there’s a growing list of failures, recalls, and breakages, often the result of chasing ever-lower weight and better aero performance. These opposing goals force compromises: thinner walls, reduced material overlap, or pared-back layups. At best, that means added cost and complexity. At worst, it risks durability and rider safety.
Some manufacturers hit these targets better than others, but they are all stuck in a vicious self-perpetuating marginal gains cycle. While it seems like the industry is forced to reach for higher and higher fruit, taking a step back it’s clear we are all on a race to the bottom. Some riders have already experienced catastrophic failures in races and training due to the increasing fragility of ultra-lightweight components. While each case is unique and some are simply the result of poor manufacturing, even then many of them may find their origins in that race to the bottom. That’s not to mention many of the fit complexities, proprietary component sourcing, and service costs many of these design updates force on the end user, as discussed in part one of this series.
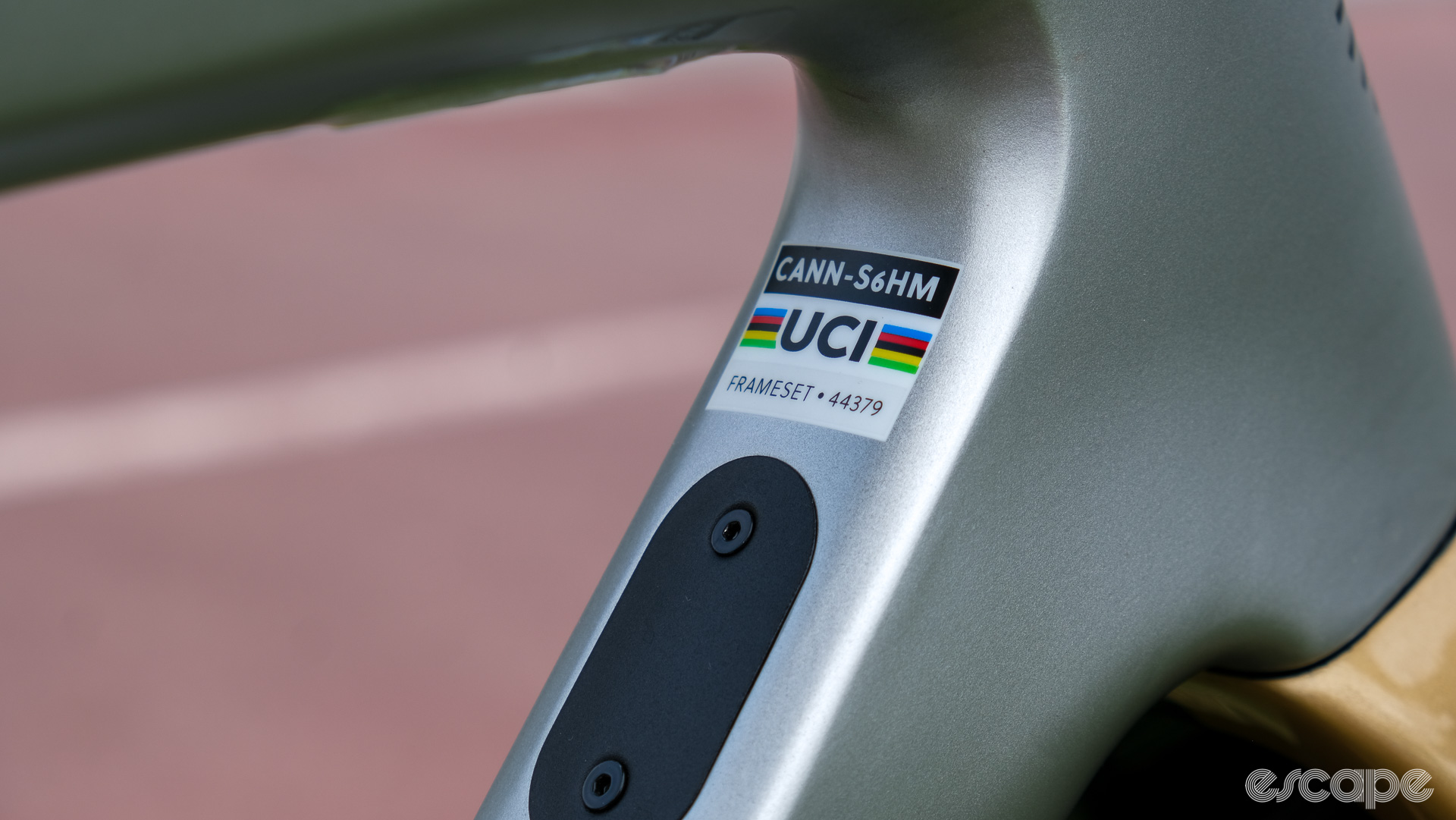
I see two alternatives, and we’ve covered both in depth here at Escape Collective.
Did we do a good job with this story?