Hello Escapees!
As a mechanical engineer who builds custom bikes as English Cycles, and as a self-proclaimed bike tech geek who loves to help clients understand elements of bicycle design, I have been invited to share my knowledge and passion in this column. My hope is to make bicycle engineering concepts more accessible and answer some of the “whys” of tech. I will endeavour to be clear with what is fact and what is opinion, and when evidence is empirical or anecdotal.
Today, I’m focusing on the basic materials and mechanics of a bike frame. I mostly build in steel, but there are many materials equally suited for creating a great ride. In truth, the design is the difference, as long as the material properties are correctly factored in. So be wary of sweeping statements such as “steel is comfortable” or “carbon is stiff”.
Let’s first take a look at some material properties, starting with the modulus. A measure of stiffness, the modulus is defined as how much a material deflects under load. Metals, being isotropic – meaning they have consistent properties in all directions – have a fixed modulus. Alloying, which adds small amounts of other elements, can increase the strength and affect other properties, but will not change the stiffness. In a very basic sense, steel is the stiffest material commonly used for bicycles – but it’s a bit more complicated. We’ll come back to that.
So, what about carbon? Whilst we generally refer to this material by the name of a single element, the material actually being used is carbon fiber reinforced plastic (CFRP). The fibers by themselves are not a structural material that can handle compressive loads (though they can support tension as a simple yarn or rope), and the resin (plastic) has low strength and stiffness compared to the fiber. However, once the fibers are laminated into the plastic matrix, the resulting composite can have very useful properties. (It should be noted that the term “composite” can be used differently within the bike-building realm. For example, a “composite” fork could be made from CFRP or from an aluminium crown with steel legs. Bike historians: Reference the Pace RC30 composite fork from 1989.)
Technically, carbon composite can have a higher modulus than steel, but it’s typically only able to achieve this high stiffness in one axis, depending on the “layup,” which describes the direction of the fibers arranged in the matrix. The problem is this: In order to achieve the directionally balanced properties required to be suitable for a bicycle, the fiber layup is usually in multiple axes. Currently, this method makes it very challenging to create a CFRP tube as stiff as a steel tube might be in any one axis. So, while CFRP might be stiffer in a single axis than steel, that’s because of the layup, directionality, and amount used more than the material itself.
Returning to the other commonly-used metals: Titanium has half the stiffness of steel, aluminium one-third. But a material’s modulus is only one aspect of many that affects the stiffness of a tube. Other aspects include diameter, wall thickness, and shape. Diameter gives the most bang for your buck – the stiffness of a tube increases with the fourth power of the radius; this is one of the reasons why aluminium frames use such oversize tubing to compensate for the inherent low stiffness of the material. The wall thickness has a more linear relationship with stiffness. Meanwhile, shaping can allow for directional increases in stiffness – such as ovalising to make the effective diameter greater in one plane, or perhaps smaller in another.

So, what’s the takeaway from looking closely at material properties? It becomes clear that one can design and build a frame from each of these three metals that, when tested on a static jig for deflection, would have exactly the same stiffness. Of course, such a basic load-deflection test is only part of the picture – the design and material of a frame may add other aspects that affect ride quality, such as vibration absorption. But it is a useful tool to quantify the stiffness of a frame under different loads, and begin to correlate that data with the subjective experience of what the frame feels like when ridden.
Which brings us back to designing for the chosen material to create the desired outcome. In a conventional diamond frame, the front triangle is a single-plane structure, and thus its stiffness is dependent on the inherent properties of, primarily, the down tube (the top tube helps too, but it is the down tube tying the bottom bracket and head tube together). This is where a lot of the ride ‘feel’ will come from.
When I first started building, I spent a lot of time cutting frames up and then brazing in different tubes in order to understand the amount of torsional stiffness that feels right to me for a good-handling frame. By torsional stiffness I am referring to the twisting load that happens through a frame; the resistance to this loading will keep the front and rear wheels in the same plane.

For a given size and weight of rider I think there is a sweet spot for torsional stiffness. My testing showed me that with undersized tubes the bike rode fine until I was pushing hard on corners on a descent. Then the front end would feel a bit vague and would not inspire confidence. With oversized tubes, on rough roads the front end would skip and bounce as it tracked. But at the right size, there is sufficient stiffness for the frame not to twist much under hard rider input, but enough flex for the wheels to have a little independent tracking to preserve road-holding.
Fortunately the bike industry is starting to move away from the ‘stiffer is better’ paradigm, and compliance is being talked about. Unfortunately, there are still a lot of statements made without supporting data!
Consider the rear triangle of a frame. A triangle is, by definition, a rigid structure. If it is being suggested that there is movement here to reduce transmission of impacts, then it would be useful to see deflection data to support those claims. Conversely, a cantilevered structure can flex under load – so a long seatpost made of a lower-stiffness material can provide measurable movement at the saddle which can help make a bike more comfortable.
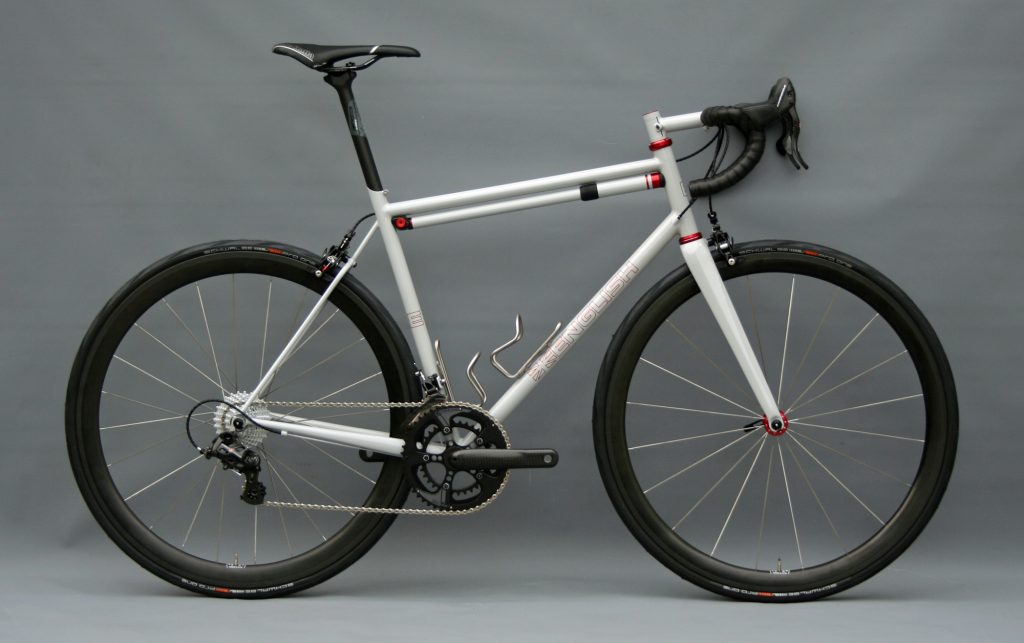
There are many other considerations when choosing a frame material: fatigue strength, joining and forming options, corrosion resistance, weight, price, aesthetics, ease of repair and ability to recycle, to name a few. But ultimately it is the design that determines the ride properties. Regardless of the material, it is up to the engineers and designers to correctly apply that material and the manufacturing parameters correctly.
I tried to make this an introductory piece to get things started – hopefully it will raise many more questions which I will do my best to answer. I’ll be back on a regular basis to continue to explore the whys of what we experience when riding, and offer some insights into the process of bicycle design.
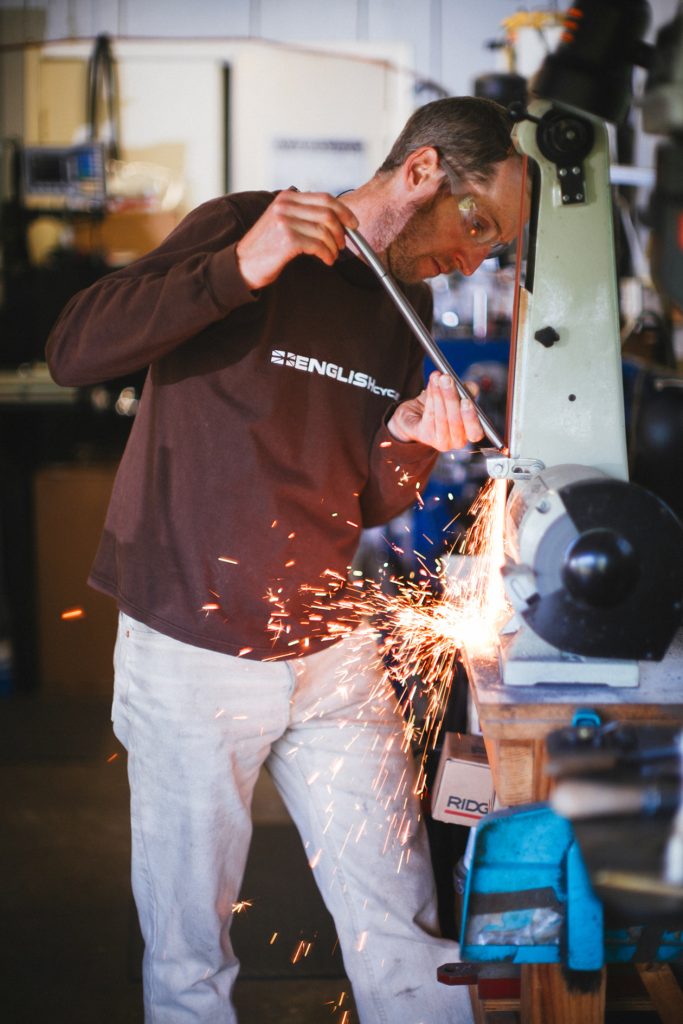
What did you think of this story?