Editor’s Picks +
News + Racing +
Newsletters
Get the latest news from Escape Collective
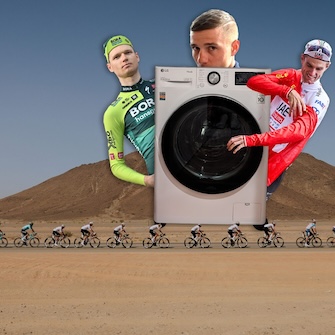
Spin Cycle
Get our unique spin on news from the world of cycling.
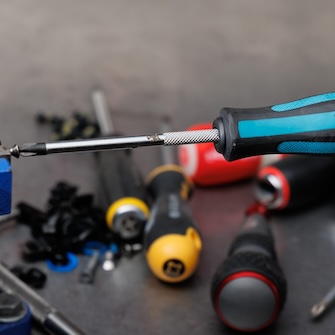
Threaded
Tools and techniques for all the mechanics out there.
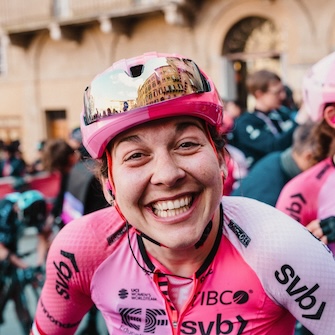
Wheel Talk
The latest news and analysis from the women’s peloton.>
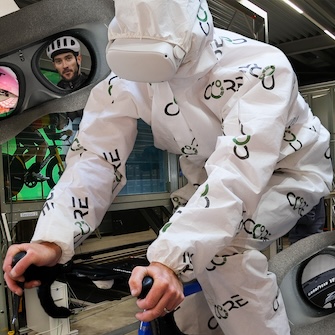
Performance Process
Better, faster, more aero.
Search bikes, parts and accessories for sale on a single site.
Top Categories
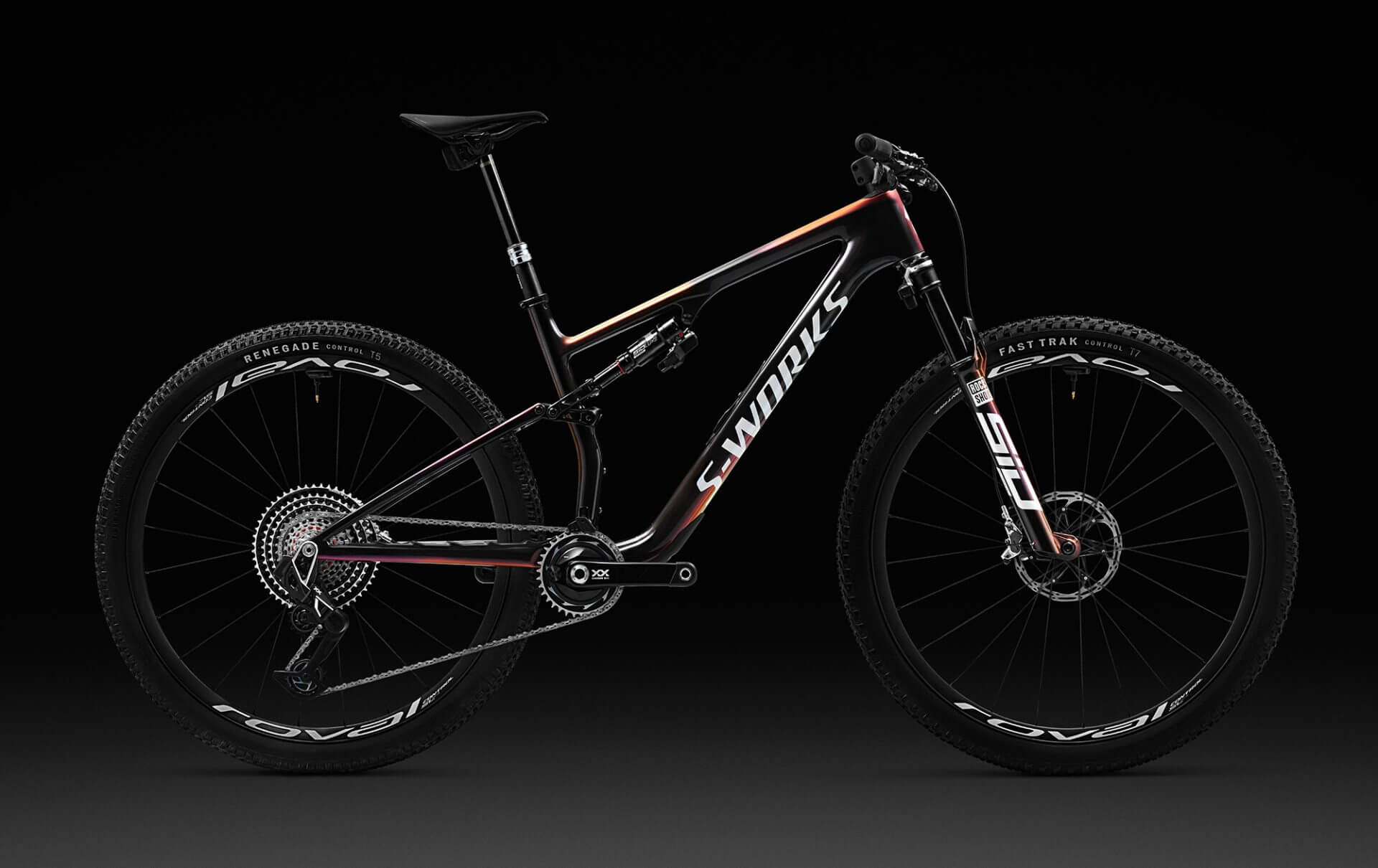
Bikes
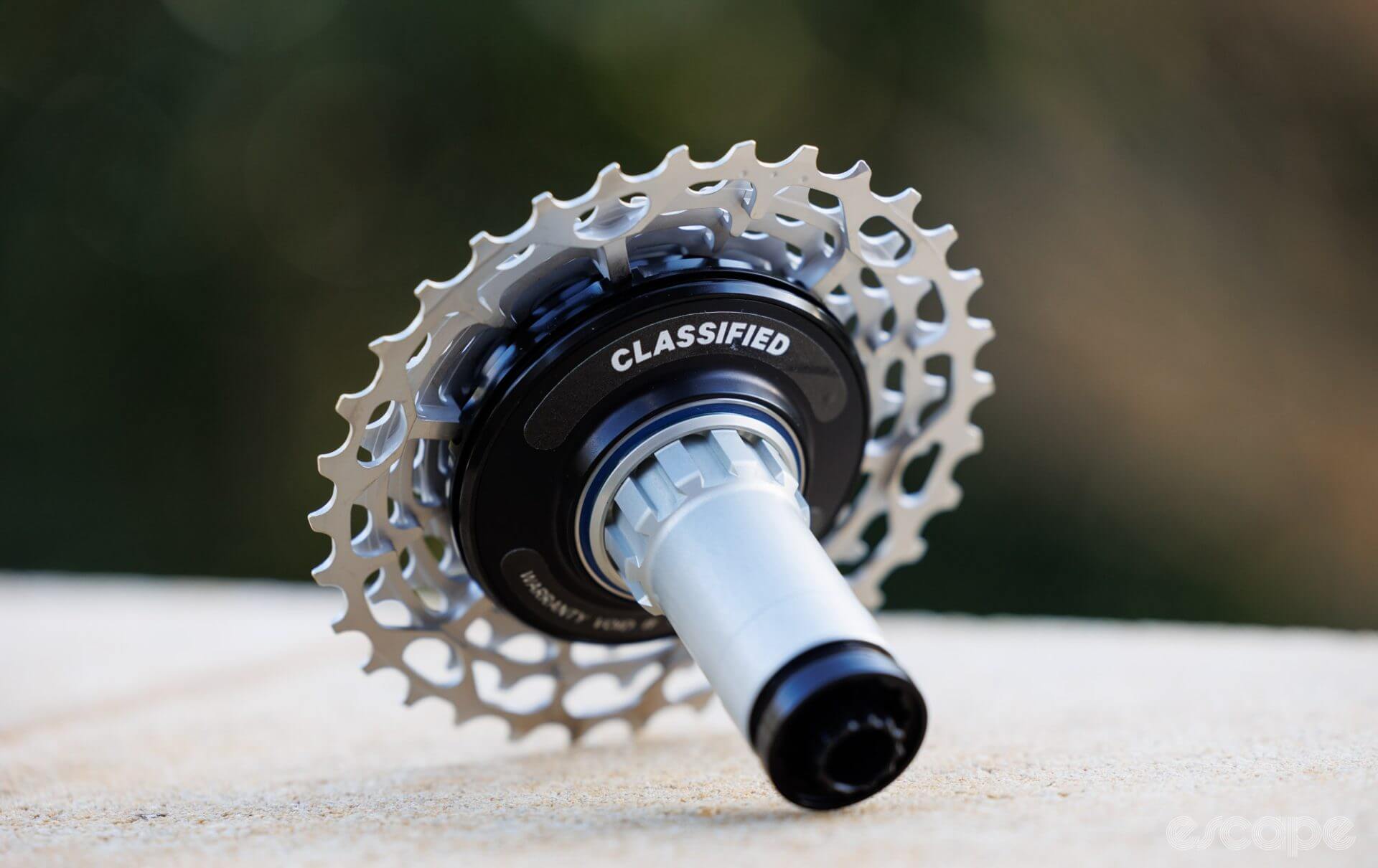
Components
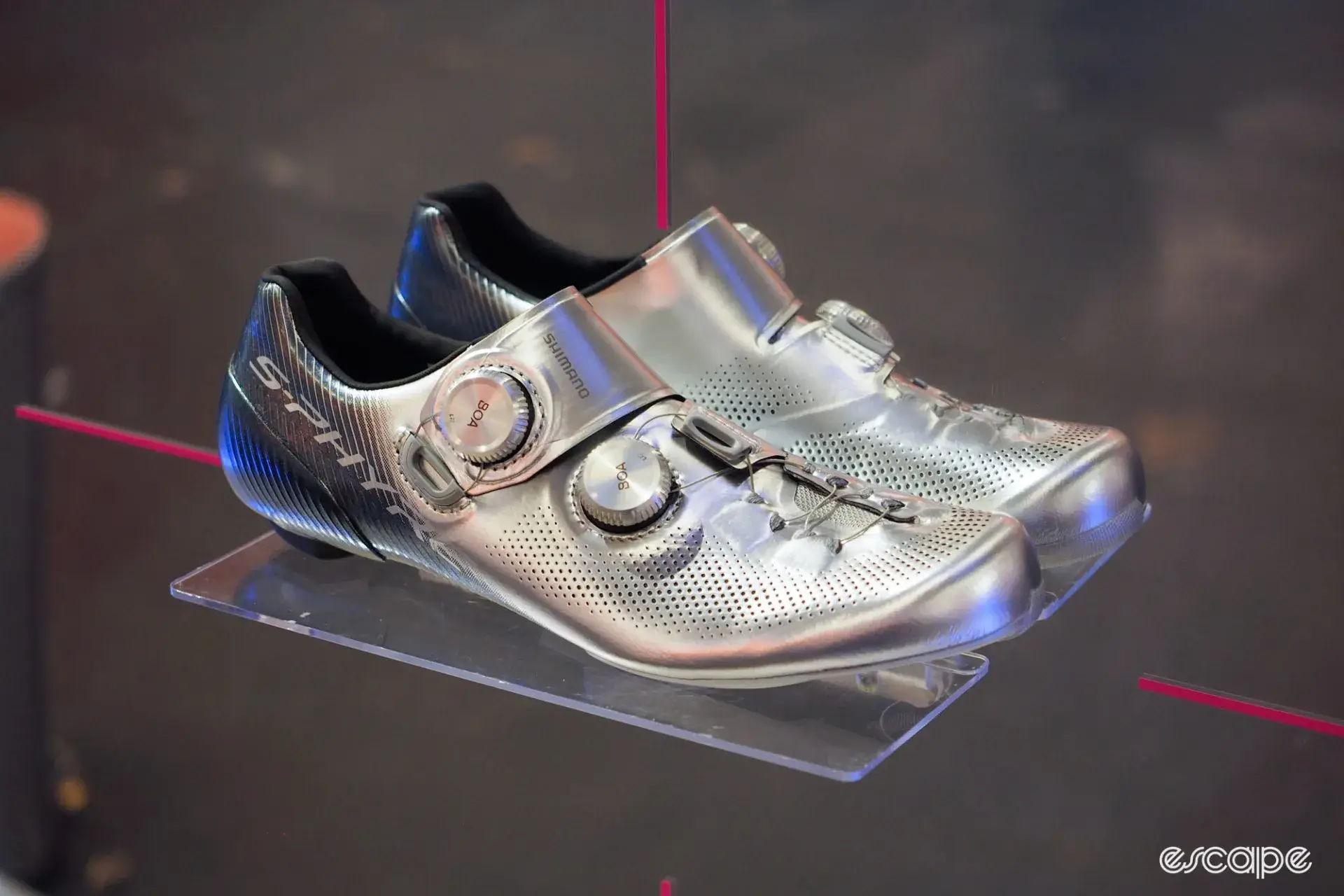
Top Comments